Custom Metal Stamped Parts for Aerospace & Aircraft
China Plate Contact has been a trusted manufacturer of metal-stamped parts & components for over 78 years for OEM and tier manufacturers in the aerospace and aircraft industry. Our stamping services give us the capacity to supply metal stampings for aerospace, including electrical contacts and connectors, along with busbars, terminals, fasteners and shields with the tight tolerances needed for communication, interconnection, electronic and electrical systems.
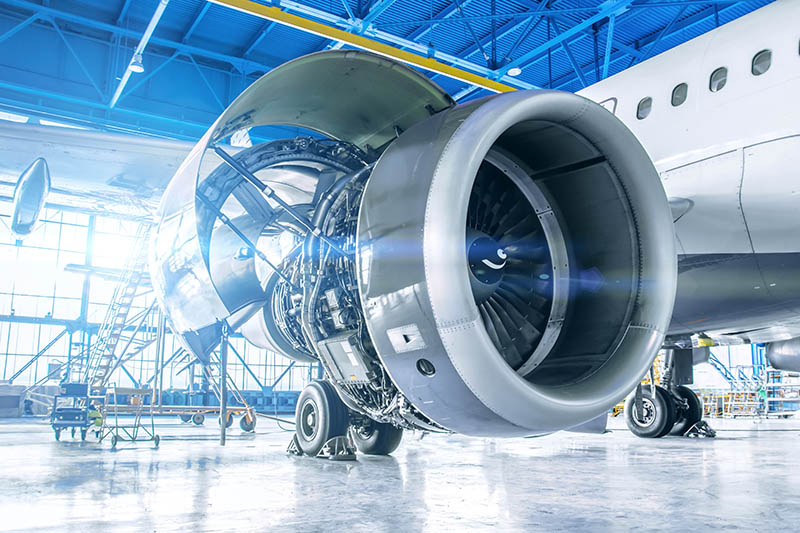
Aircraft Components Stamping
Our attention to the precision needed in the aerospace industry translates into the timeliness and accuracy our customers need in aerospace metal stampings suitable for applications such as flat connection systems, signal and power systems, headsets, handsets, press-to-talk systems and power distribution systems and controllers to name a few. We work with our customers during every step of a project, from concept to completion, and offer expertise in every phase including engineering, prototyping, tooling, production and inspection.
Having worked with the aerospace industry over a period of decades, our processes and equipment allow us to create metal parts with thorough attention to detail and accuracy, while in the shortest lead time possible to meet our customer’s needs. We’re proud to say that our processes and products in both primary and secondary operations are known by our customers throughout the industry and across the world.
China Plate Contact leverages the latest technology to ensure efficient aircraft component stamping while achieving a goal of zero defects for all our customers, especially those in the highly precise aerospace industry. We take pride in our history of supporting our customers’ needs long term and work on creating business relationships that foster mutual success.
Metal Stampings for the Electric Aviation Industry
China Plate Contact is your trusted partner for metal-stamped parts, with over 82 years in the industry. To produce high volumes of identical parts, more manufacturers are turning to metal stampings for electric aviation. There is an increasing desire for electric motors in aviation, and our team offers a cost-effective solution to assist businesses in reaching their goals.
Demand for Electric Aviation Metal Stampings
In recent years, the rising demand for electric aircraft has increased the need for electric aviation metal stampings. Following your specific configurations, we take sheet metal and turn it into parts the aircraft requires with several capabilities to meet demand.
Progressive Die High-Speed Stamping
We incorporate state of the art vision systems and sensor technology on all our presses to ensure 100% quality control. With Bruderer presses and sensor technology, we produce your metal stampings for electric aviation with 100% quality control. Quick turnaround makes your project cost-effective, with features such as:
- Coating and precious metal plating
- Embossing and inlaying
- Numbering
- Multiple stamping
- Reeling and threading
High-speed stamping reaches up to 1,500 strokes per minute. Our in-house tool room ensures we can meet your intricate design requirements. We stamp aluminum, copper-based alloys, exotic metals, and ferrous metals at high speeds for electric aircraft.
Progressive Die Heavy Stamping
Progressive die heavy stampings for electric aircraft use Minster technology. Features include:
- Countersunk
- Shape critical
- Compliant pin
- Strain relief
- EB welded
Common materials used for heavy stamping services are copper, steel, aluminum, titanium, and beryllium copper. Even with complex tooling requirements, we stamp your electric aviation parts with precision.
Parts Made with Metal Stampings for Electric Aviation
The electric aviation industry calls for specific components to meet current trends and requirements. Custom electric aircraft component stamping at China Plate Contact includes parts such as anodes, brackets, fasteners, lead frames, and cable connectors. Aviation customers also benefit from compression limiters, rolled bushings, shields, selective-plated lead frames, and busbars.
At China Plate Contact, we can complete your jobs from start to finish, on time, with our essential additional services.
Die Design and Manufacturing
To reduce costs and increase satisfaction, we produce dies in-house. Our engineers have the experience to maximize productivity and make the manufacturing phase run smoothly.
Assembly
Hardware components and plastic and metal inserts are easily assembly and attached to metal stampings for electric aircraft with our secondary semi-automated and in-die assembly services. Highly skilled on-site engineers provide recommendations for successful production.
OUR PRODUCTION PARTS
China Plate Contact produces a variety of precision metal stampings made from copper, precious metal and ferrous metals. We specialize in the manufacturing of both precision electrical connectors and non-electrical parts that are used in our world’s most demanded consumer products and essentials.
Some examples of custom, precision metal stampings we’ve produced for our aerospace manufacturing customers include:
- Busbars
- Compression Limiters
- Crush Bushings
- Fasteners
- Engine Components
- Inserts
- Lead Frames
- Rolled Bushings
- Selective Plated Lead Frames
- Shields
- Terminals, Contacts and Connectors
- Transmission Lead Frames
Materials
- Copper
- Brass
- Phosphor Bronze
- Beryllium Copper
- Steel
- Stainless Steel
- Carbon Steel
- Aluminum
- Galvanized Steel
- Titanium
- Platinum
- Inconel
- Hastelloy
China Plate Contact METAL STAMPING SERVICES FOR THE AEROSPACE INDUSTRY & AIRCRAFT COMPONENTS
We Prioritize customer satisfaction
At China Plate Contact, our utmost priority is customer satisfaction with the quality and integrity of our parts. In-die sensors, press monitoring systems, camera vision systems and a dedicated inspection team ensure parts leaving the production line exceed customer expectations.
Press Monitoring
The press monitoring system tracks production OEE and offers real-time data feedback reporting from every press on the shop floor. Data collected is used to drive efficiency and eliminate downtime so raw material is processed through machines quicker, parts are coming off the presses at accelerated speeds and parts are delivered and in the hands of our customers on time. As an advanced quality measure, multiple in-die sensors and in-line camera vision systems inspect critical dimensions of all running parts at high speed and high accuracy to eliminate error and ensure the consistent delivery of quality parts.
Leading Technology
China Plate Contact invests in cutting-edge technology to drive process efficiencies and produce high-quality and cost-effective product. We operate progressive die metal stamping technology from Minster and Bruderer, the leaders in stamping automation technology and equipment. Our enhanced manufacturing equipment is capable of producing with more precision and accuracy and can achieve complex geometries and tighter tolerances. We also have a dedicated automation department that develops in-die sensor technology and camera vision systems used to incorporate quality assurance through all phases of stamping production. With a committed team, innovative equipment and superior quality control, China Plate Contact can provide progressive die high-speed stamping and heavy stamping services that turnaround reliable parts on-time and on-budget.
Building Partnerships
China Plate Contact is known for building partnerships through a “co-engineered” approach to collaboratively address design and manufacturing challenges alongside our customers. Together, with customer engineering and sourcing teams, we are routinely able to co-develop solutions and bring cost saving ideas to complex projects. It is our goal to optimize efficiency on every project by seamlessly bridging the workflow between the customer and China Plate Contact. Decades of experience has proven to us that the most cost-effective manufacturing strategies synergize the best engineering practices at both the customer and at China Plate Contact. We continually strive to be a premier service provider and invaluable resource to each customer by helping to drive efficiencies in all moving parts of a project.
Quality
With Zeiss CMMs, OGP smart scopes and dedicated sensor and camera vision system technology to monitor stamping parts in and off production lines, our customers know quality assurance is our number one priority. We are IATF and ISO certified and have a dedicated quality lab and inspection team responsible for maintaining quality control at the greatest extent.
Learn MoreOur Technology
China Plate Contact lives by the philosophy of embracing the latest technology. We have regular technology updates and new equipment acquisitions so we can always have the necessary tools to develop breakthrough techniques and processes and deliver quality parts.
Learn MoreSupply Chain Management
From the very bottom of the supply chain, we manage product material, metal stamping production, pre- and post- stamping operations as well as product handling, tactical scheduling, logistics and delivery. China Plate Contact helps manufacturing customers reduce their supply base by offering assistance in all phases of metal stamping production from early design concepts to tooling to production of finished stampings and assemblies. Customers can track projects with real-time updates and keep all teams aligned with project goals.
Learn MoreOther Industries We Serve
It’s our mission to offer premier metal stamping and metal forming solutions to the most challenging and innovative engineering product designs. We combine advanced metal stamping production and tooling equipment, superior quality controls, seamless automation and production processes and a knowledgeable and experienced team to serve an array of market segments.